Specialized equipment
The ability to innovate is an important part of Bergteamet
Working in the mining industry often means that needs arise that are completely unique. When traditional methods cannot be used or when new challenges appear, new solutions are required. Innovations have always been part of Bergteamet’s DNA and special assignments are an important part of Bergteamet’s range of services.
These are some examples of special equipment that Bergteamet has developed. Most of the equipment is based on a basic design that can then be adapted to the unique needs of each project.
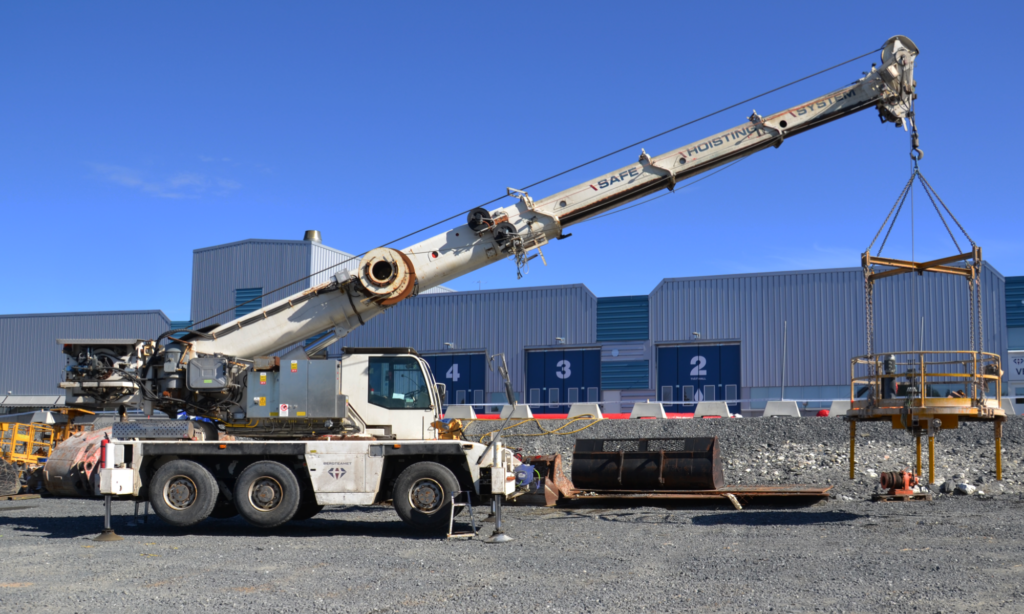
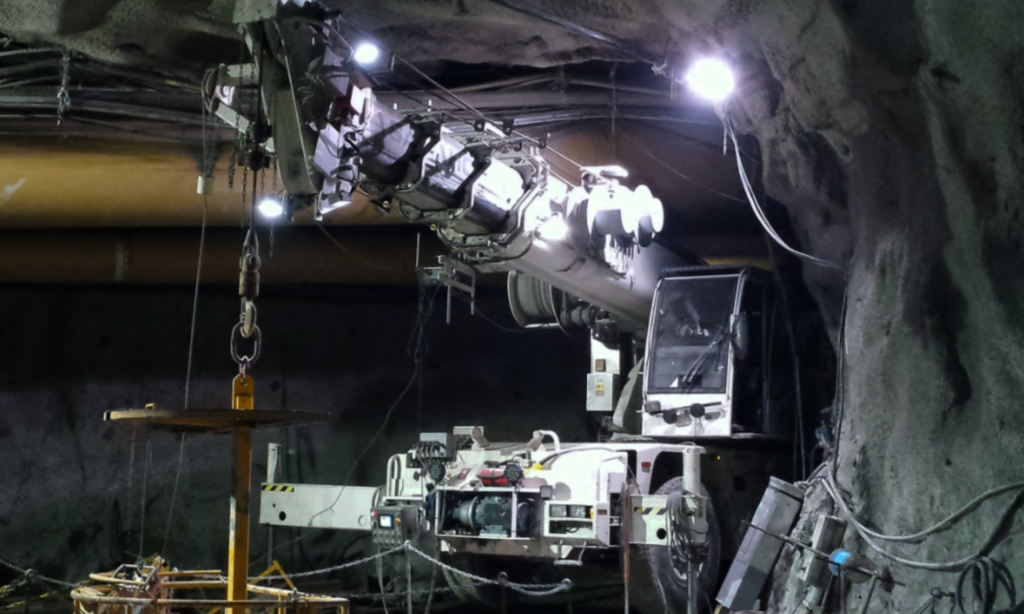
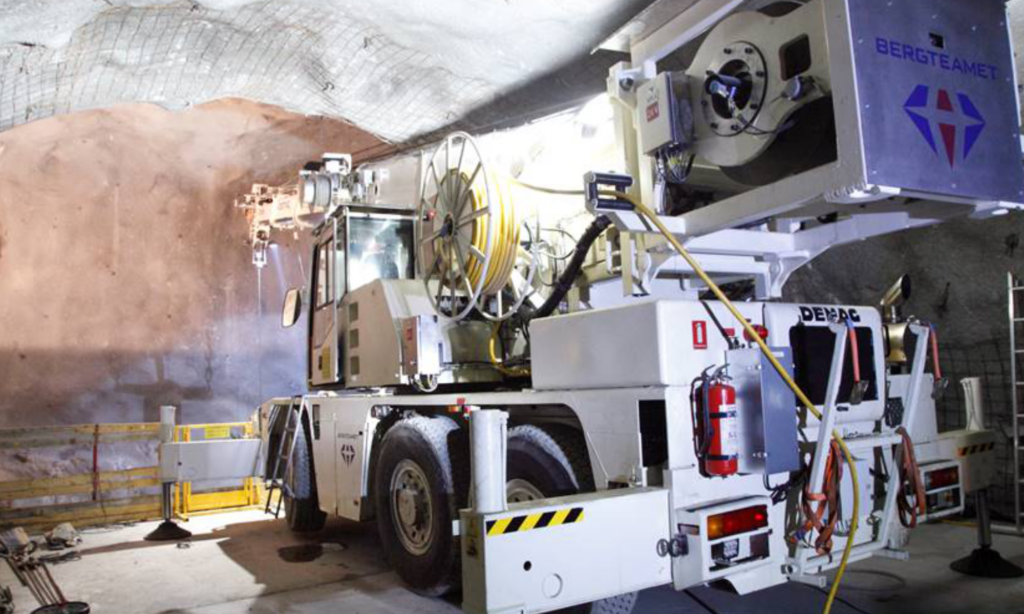
Mobile Safe Hoisting System (MSHS)
Bergteamet’s mobile scaffolding design for personnel transport is based on a standard mobile crane and handles rope-borne work platforms that are lowered into shafts for various types of strengthening, renovation and maintenance work. Depending on the nature of the assignment, the platform can consist of one or more levels and have different types of equipment mounted.
The MSHS, on the other hand, is suitable for all assignments and is approved for transporting people and manual work, unlike ordinary mobile cranes that are only approved for the transport of goods.
Shaft Cable Bolt Rig
A unique machine of its kind has been developed by the Bergteamet. It will be used for rock reinforcement of narrow shafts where cable bolts are to be installed. The Shaft Cable Bolt Rig is based on a traditional Epiroc Cabletec, a proven machine for cable bolting. The unit is complete and has all the equipment needed to drill and install cables in the rock.
With the Shaft Cable Bolt Rig we can use cable bolts that are significantly longer than the shaft’s diameter. This makes the rock reinforcement stronger and more durable.
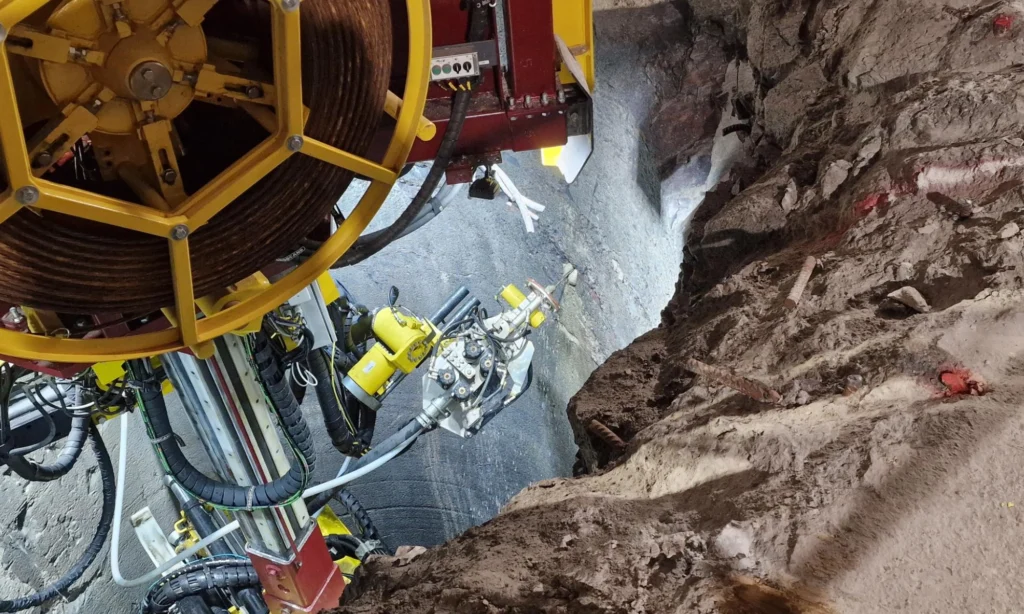
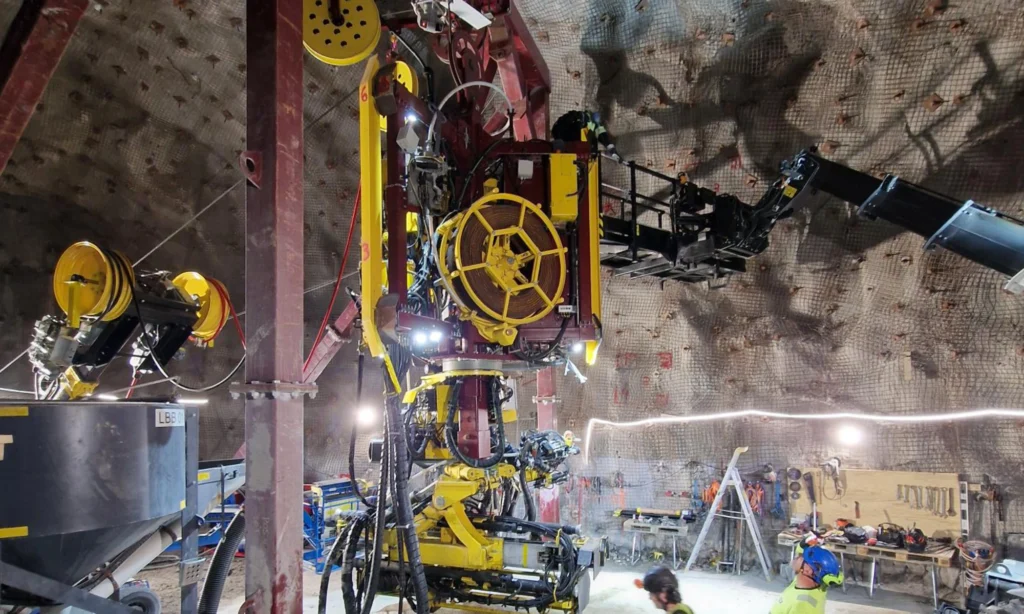
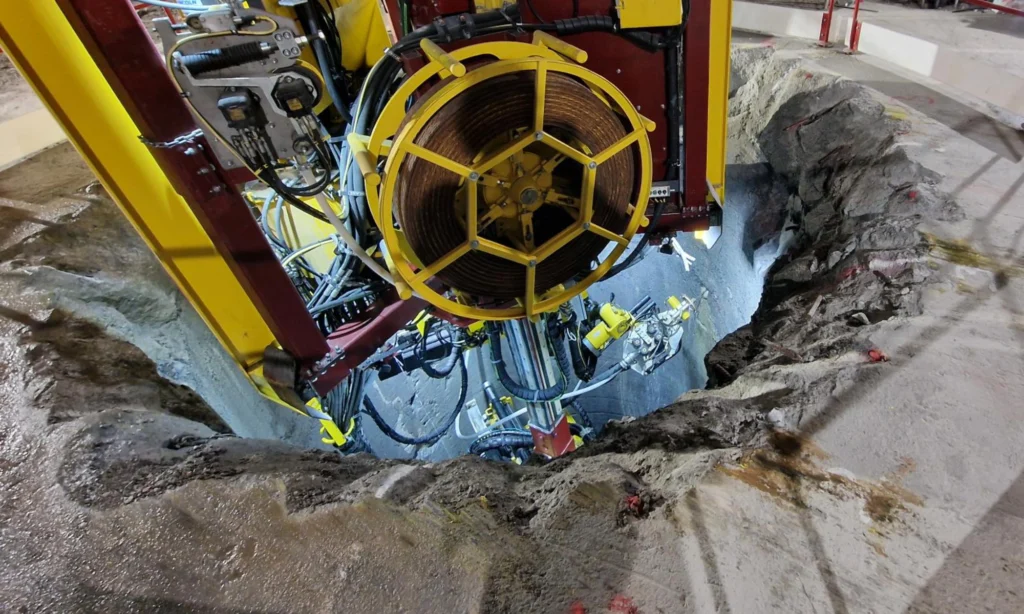
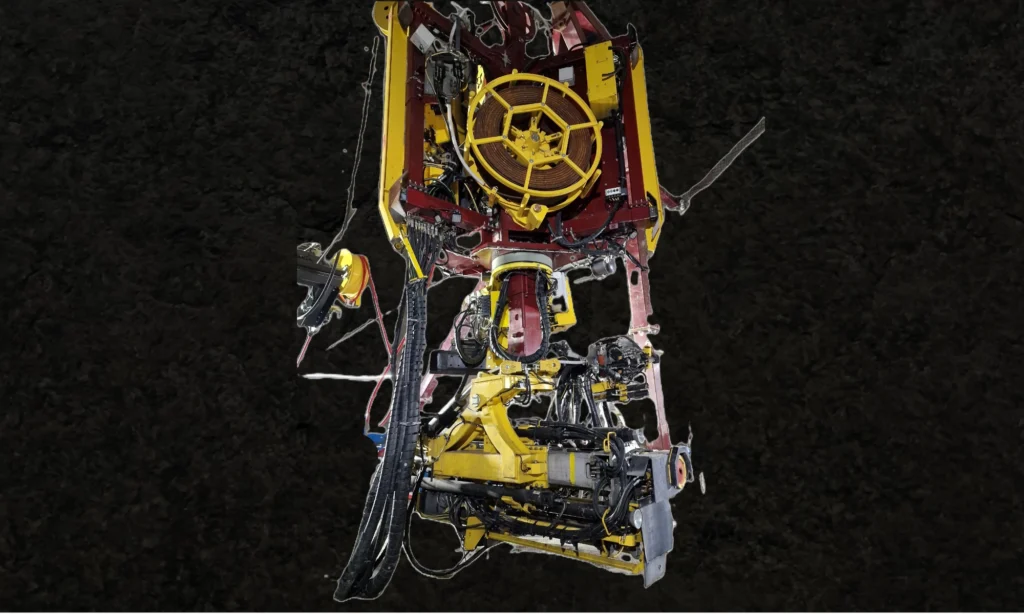
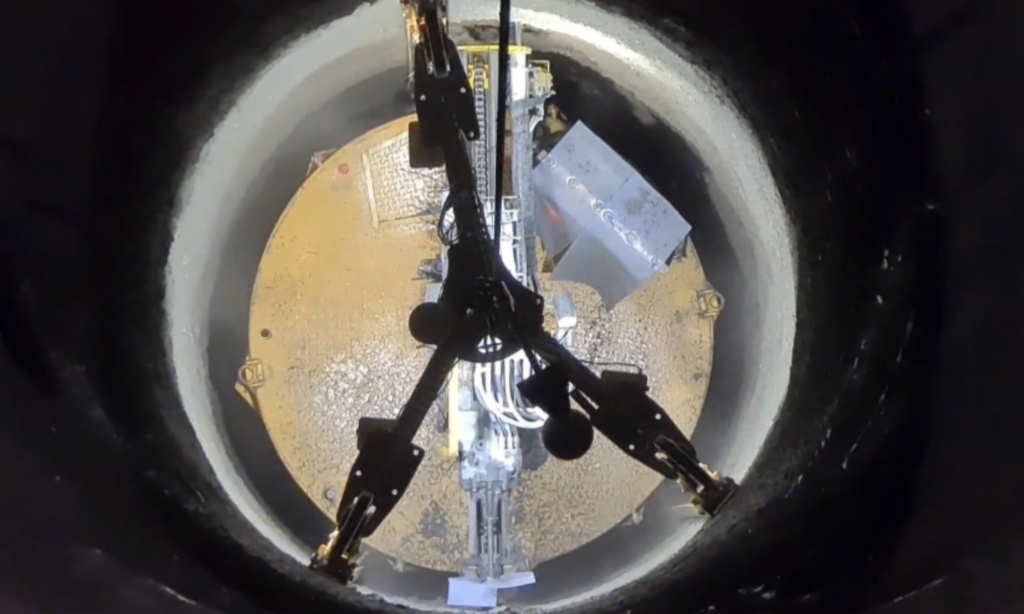
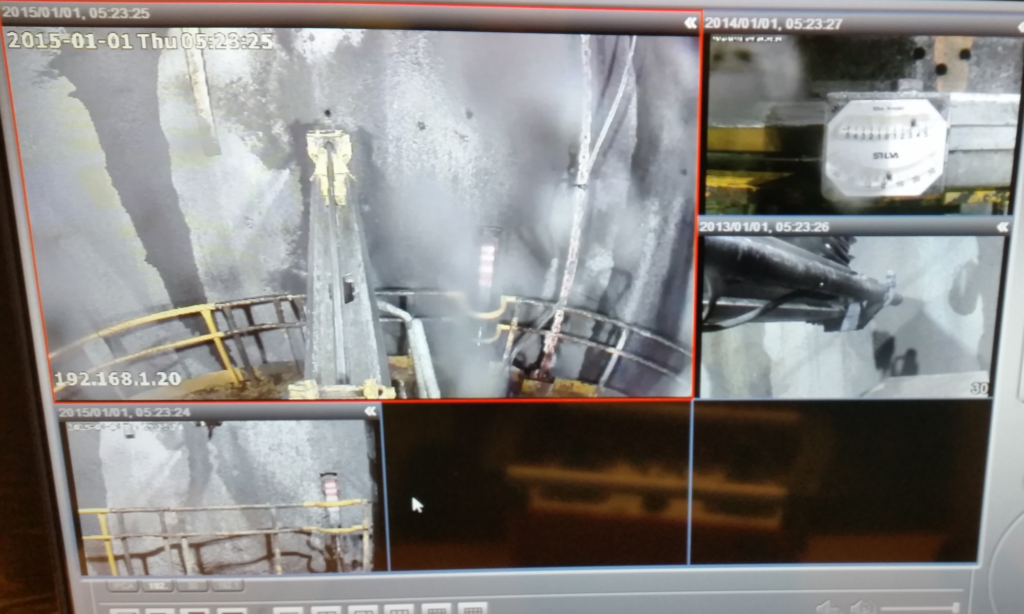
Remote controlled Bolt drilling robot
The remote-controlled bolt drilling platform is used for work in shafts. The equipment consists of a suspended scaffold with a platform where the drilling equipment is mounted. Wheels at the top and bottom ensure that the equipment runs smoothly in the shaft. The robot drills a bolt row at a time and is winched down 1.5 meters at a time.
The robot is controlled by a machine operator who sits safely and securely in a cabin near the shaft and follows the work via a monitor. The control is carried out wirelessly with a radio control.
Remote Shaft Lining Robot
The remote shaft lining equipment is a complete remote-controlled equipment for concrete spraying of shafts.
The shotcrete robot is lowered in the raise bore shaft and the wet shotcrete is transported to the spray nozzle trough hoses connected to the cable where it is mixed with accelerator and sprayed onto the shaft wall.
With support legs, the robot is continuously centred in the shaft throughout the work. The spray robot is controlled and monitored by a remote operator and eliminate the need of workers in the shaft.
The equipment has a range of up to 350 meters as standard, but in a special assignment with good conditions a record of 630 meters was set.
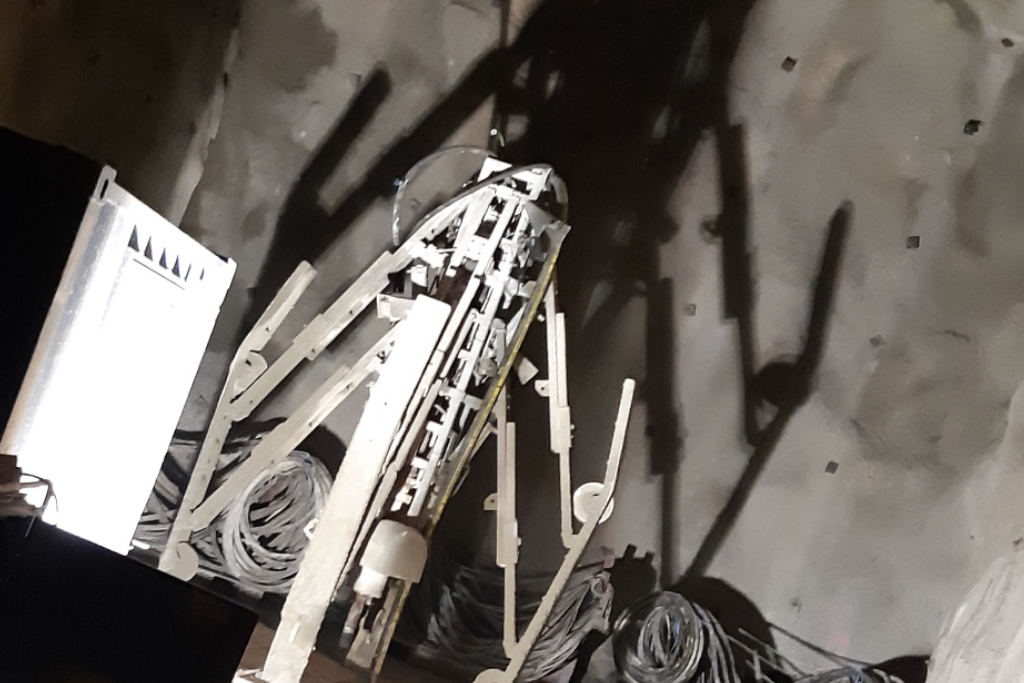
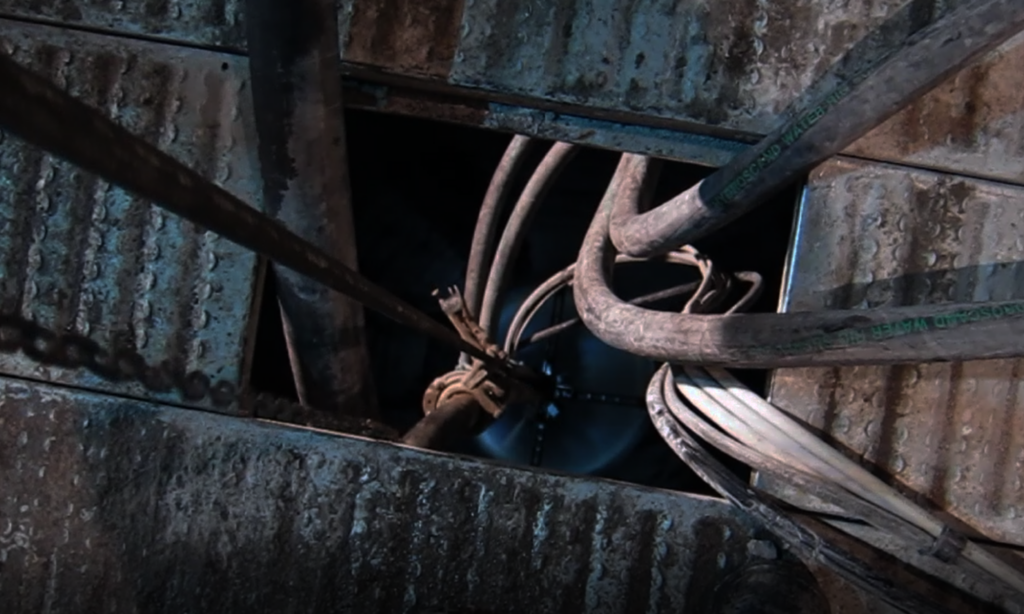
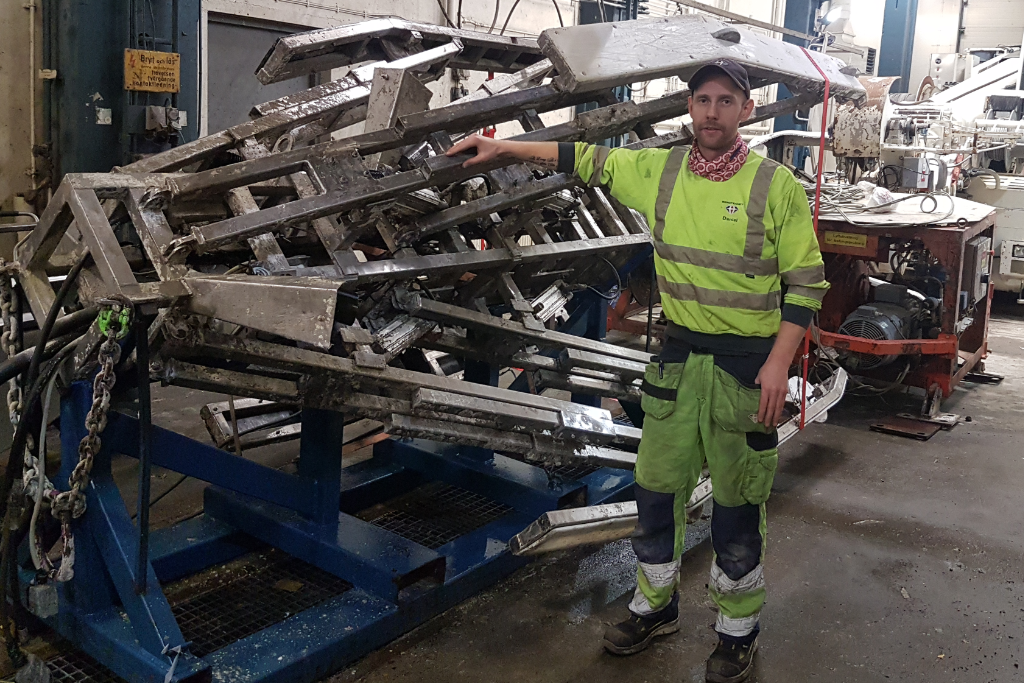
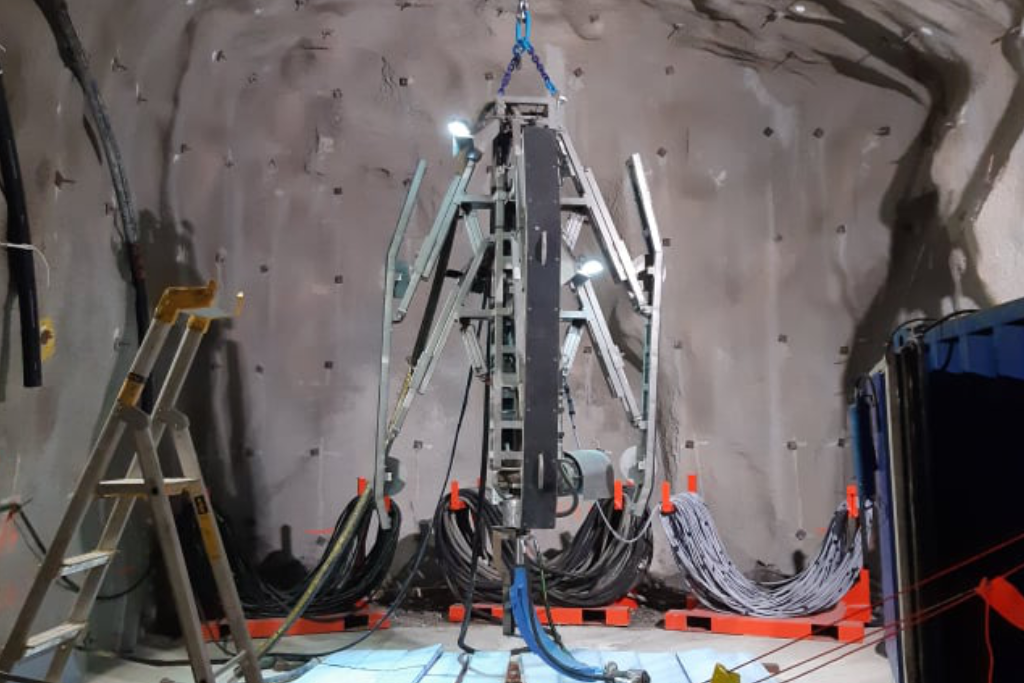
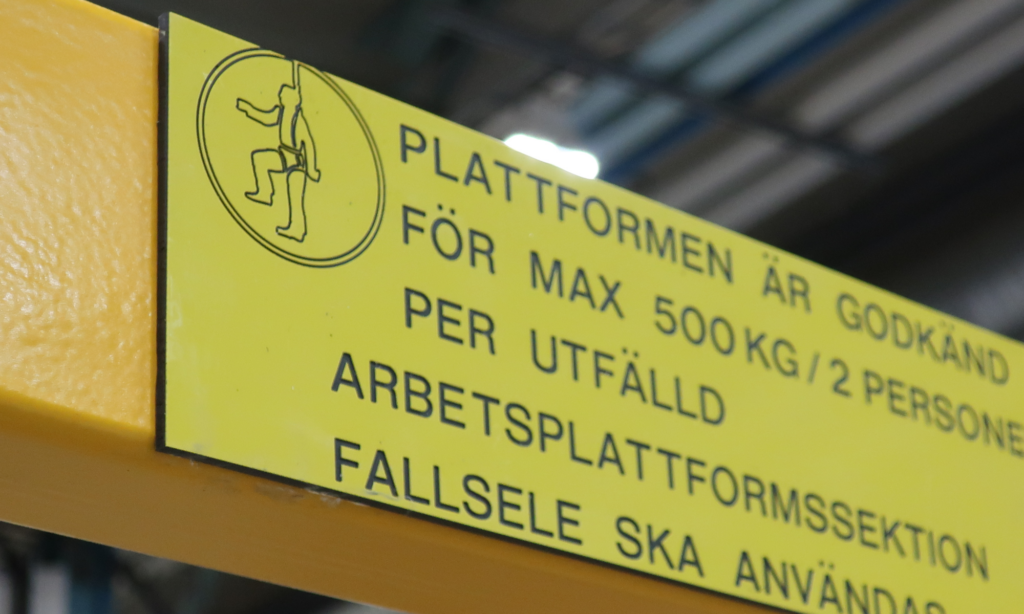
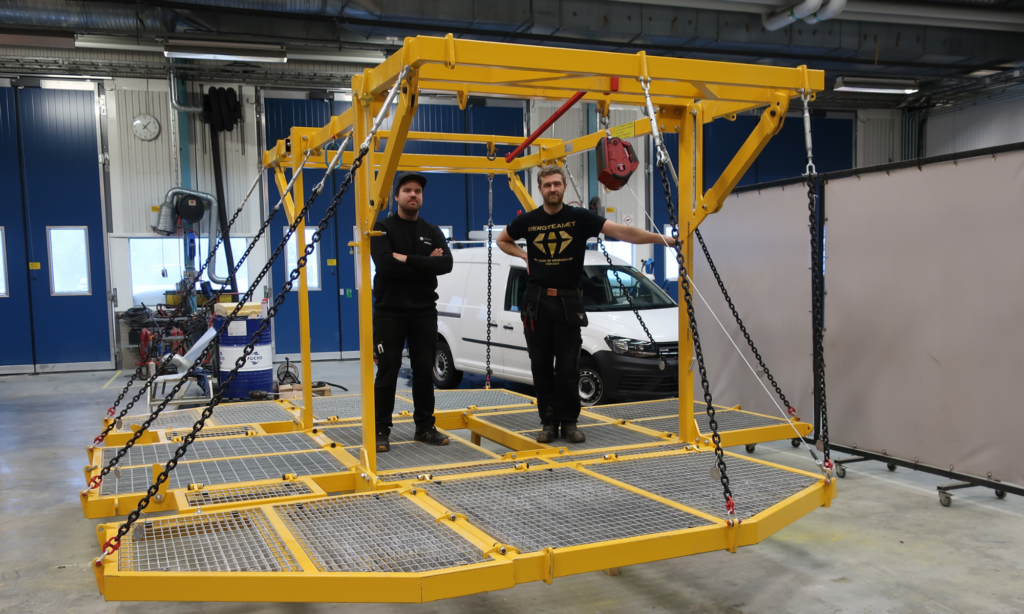
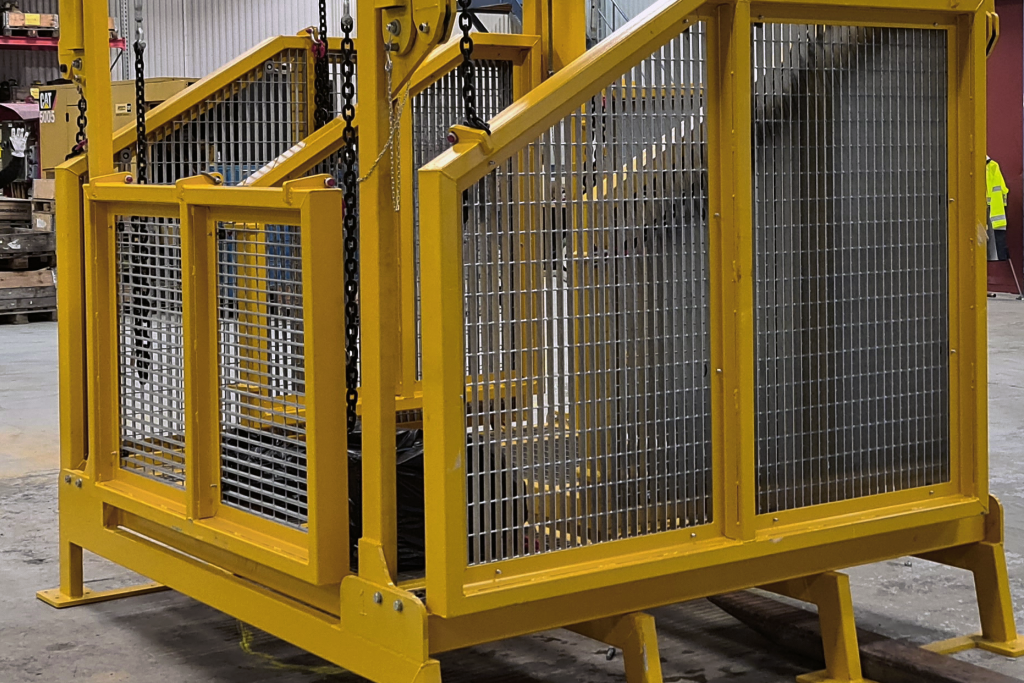
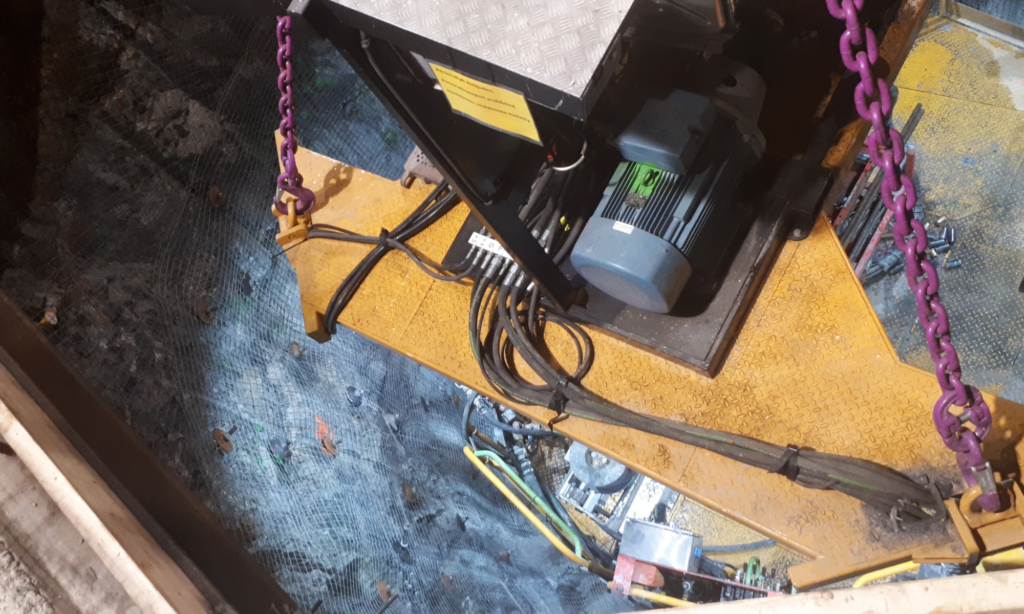
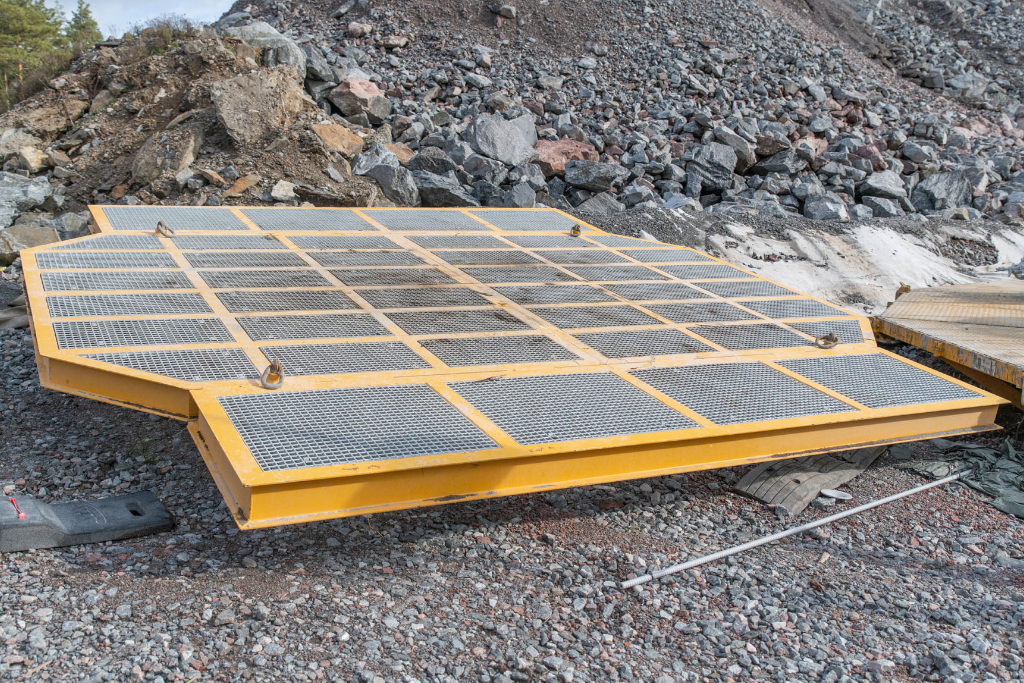
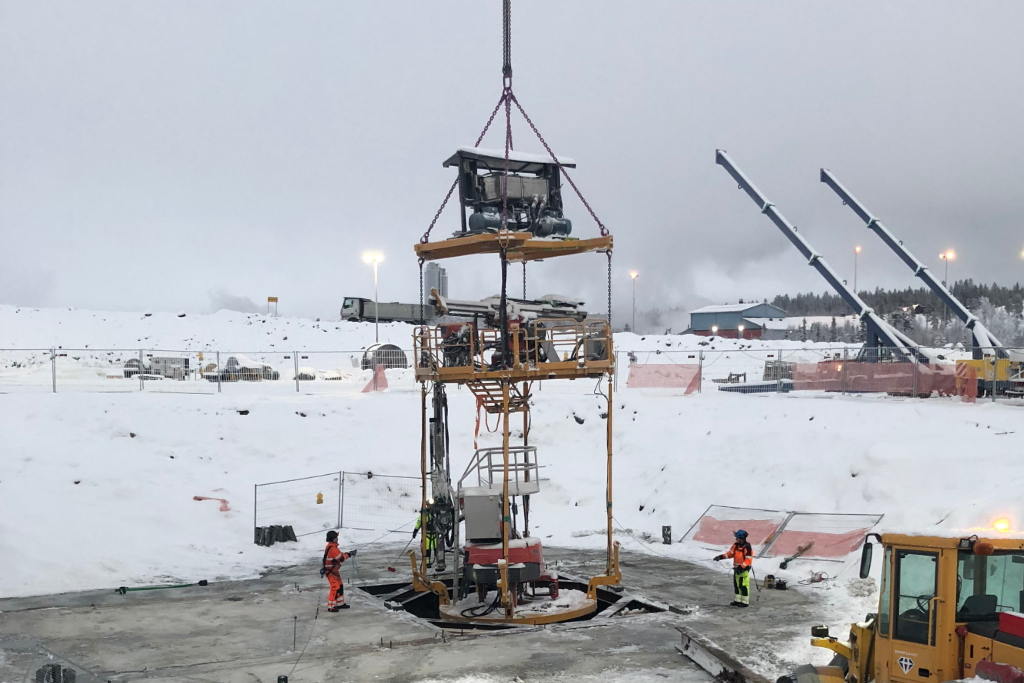
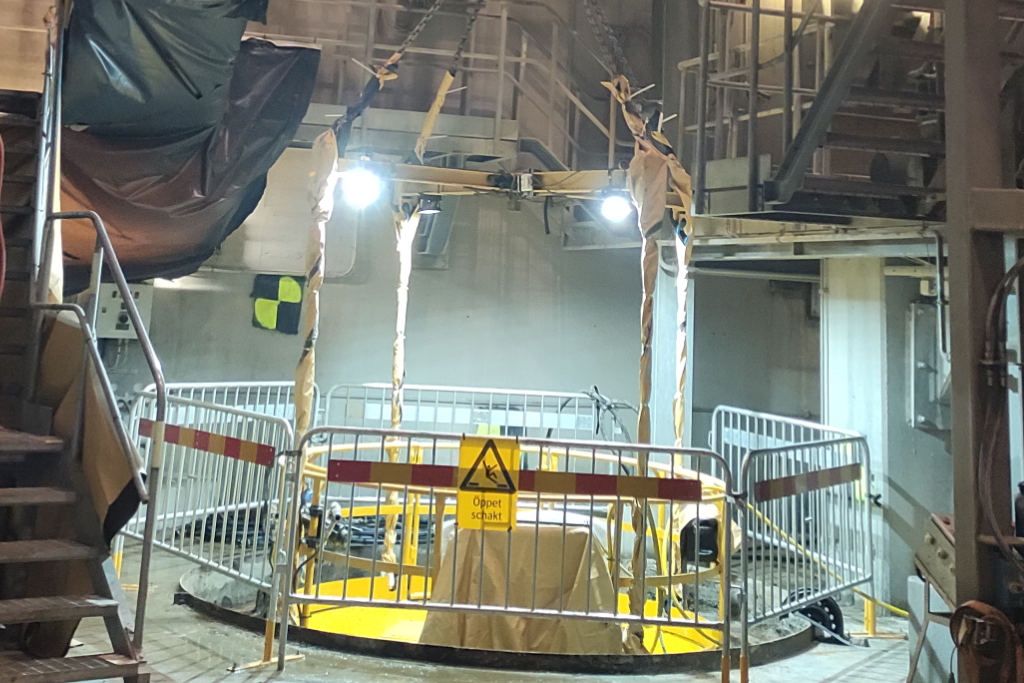
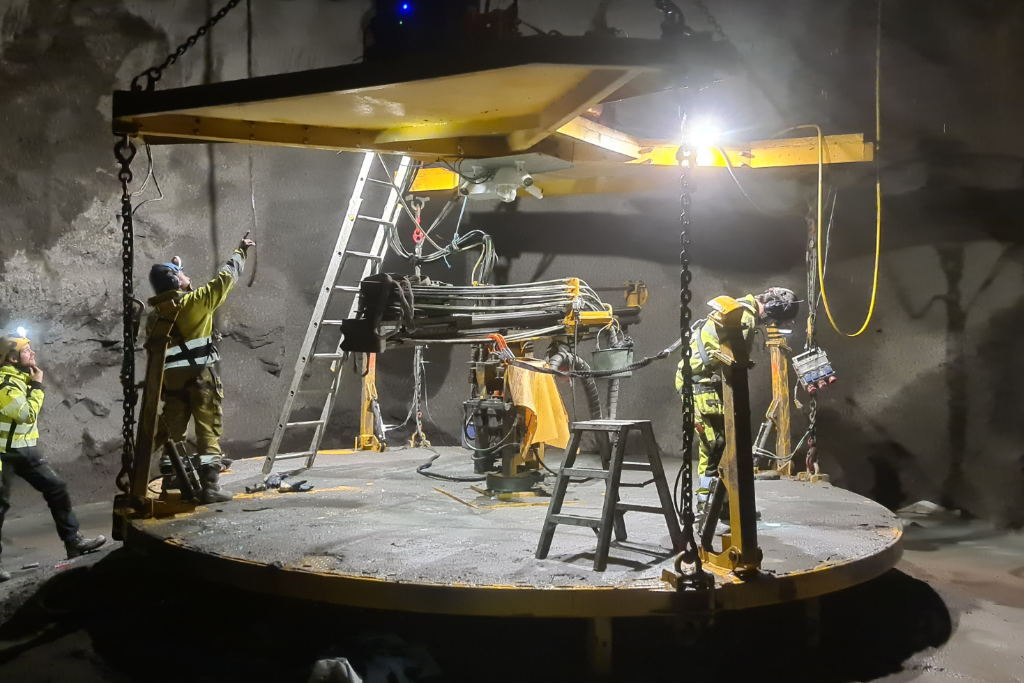
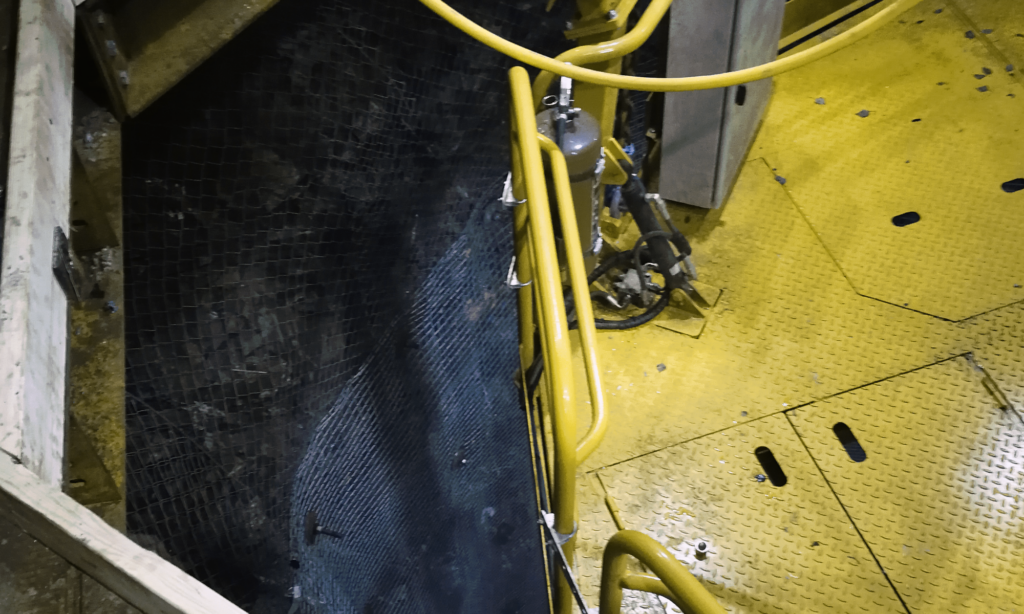
Platforms
We have several platforms for different types of assignments. The platforms are adapted and built for each new assignment to be able to carry out the assignment in the safest and most efficient way.
Underwater camera solution for filming in extreme conditions
In order to be able to inspect water-filled boreholes at great depths, Bergteamet in collaboration with GMK has specially manufactured a camera housing that can handle underwater filming up to 80 bar pressure, which corresponds to a depth of 800 meters. The robust housing is made of aluminum and has openings for both the camera lens and a light source. The housing is adapted for a GoPro camera and enables filming and photos in 4K resolution for maximum detail.
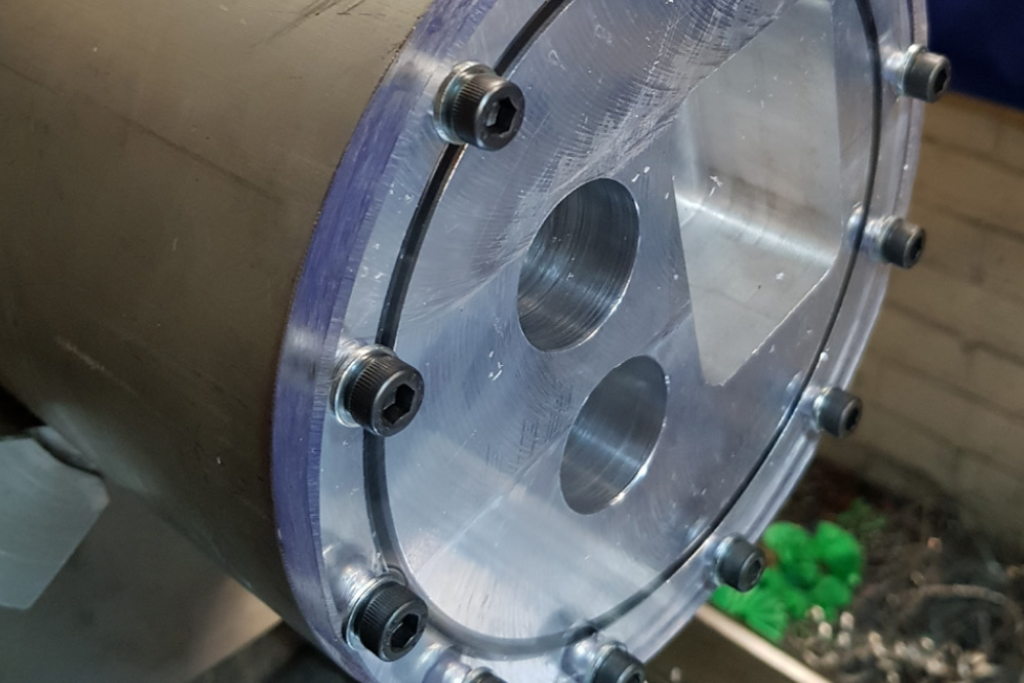
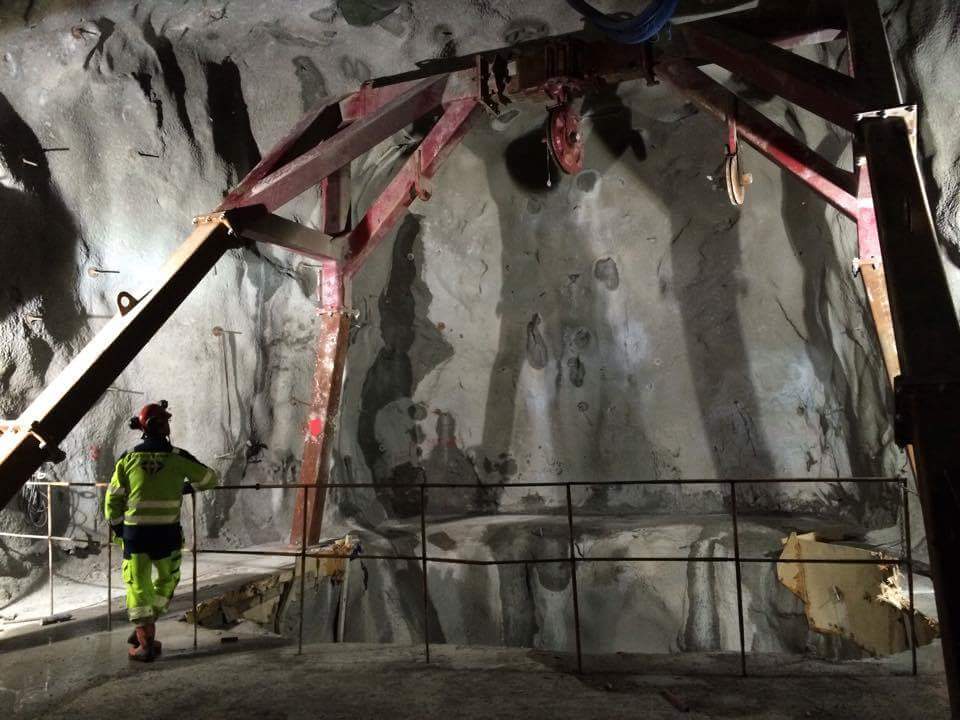
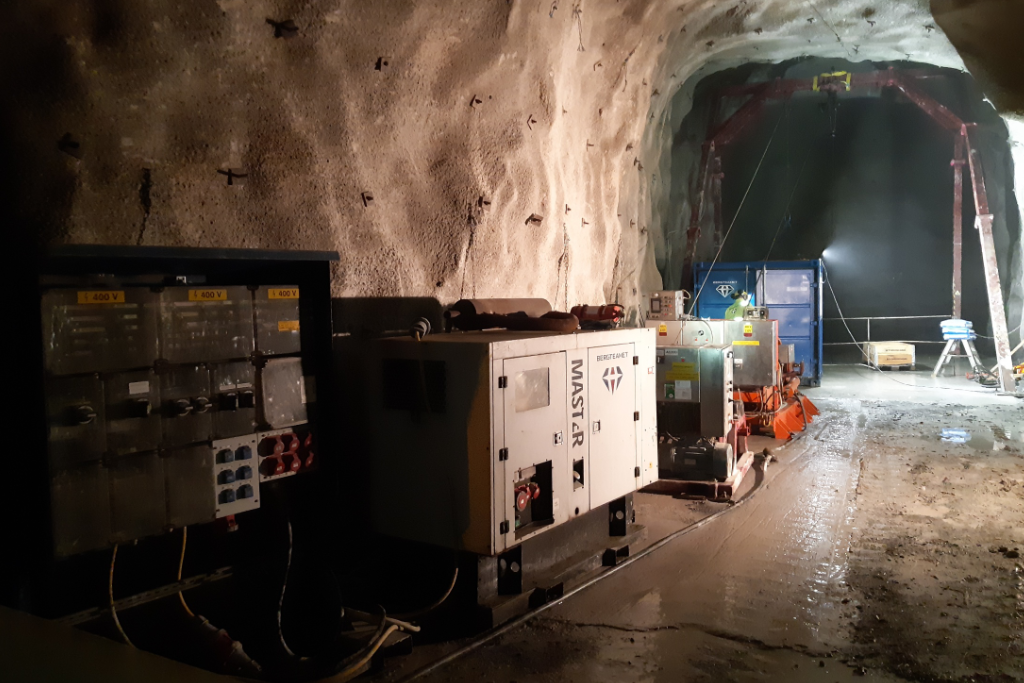
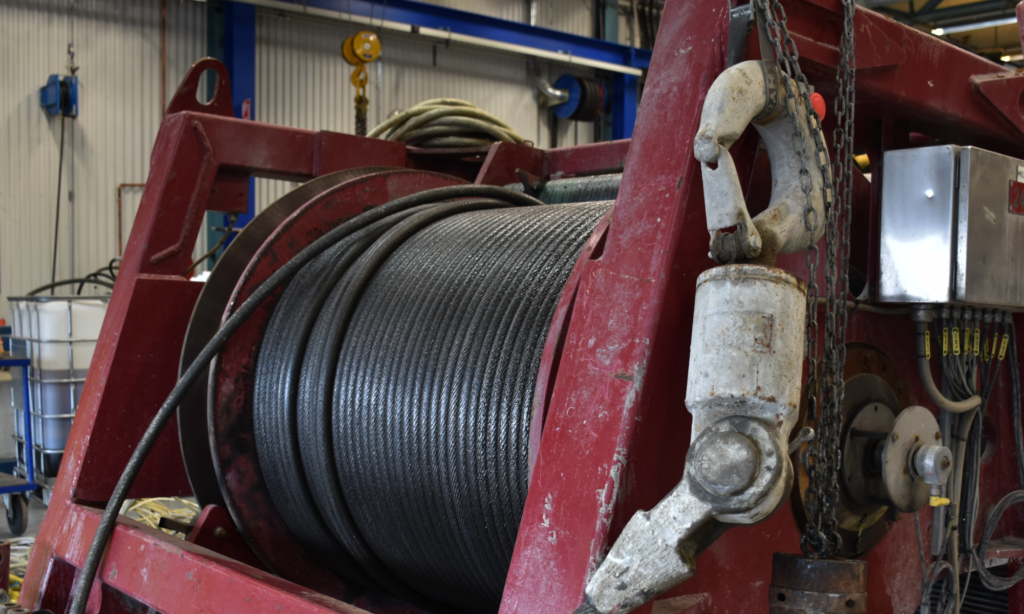
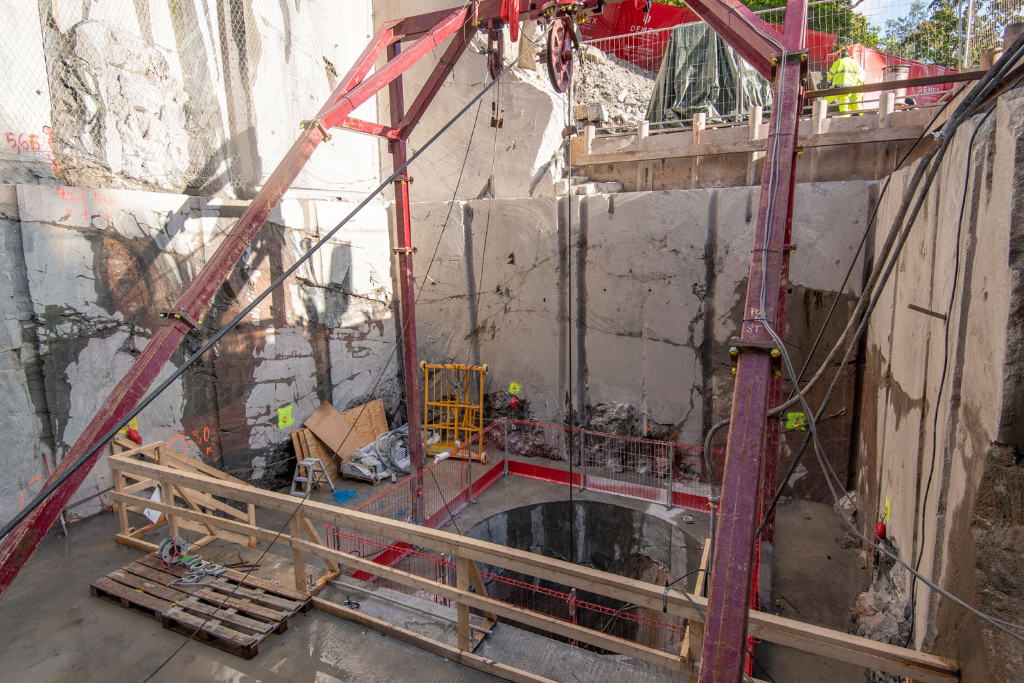
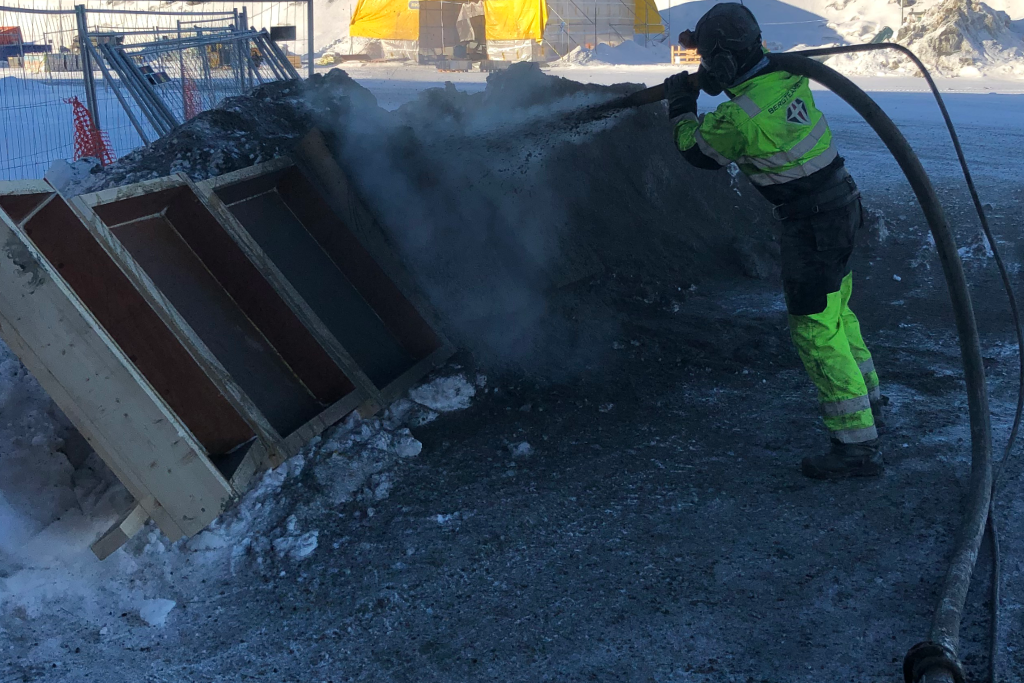
Hoist winches, shaft scaffolding, power generators and much more
We have a large range of equipment for various tasks and we also have a spare parts warehouse. It is an important component of our flexibility and ability to find new solutions.
BRAGS
When Bergteamet develops and produces equipment, the starting point is always the BRAGS guidelines.
We are a leader in the industry when it comes to safety, innovation and technology solutions. We always follow BRAGS to ensure that we have equipment that meets today’s requirements for safety.
ABOUT BRAGS:
BRAGS is an industry guideline for mine hoists and winches that has existed since 2001, but its roots go back to the 1970s. BRAGS has been developed together by the companies in the Swedish mining industry. BRAGS provides information on the design, installation, inspection, operation and maintenance of mine hoists, rescue hoists and stages suspended by ropes.