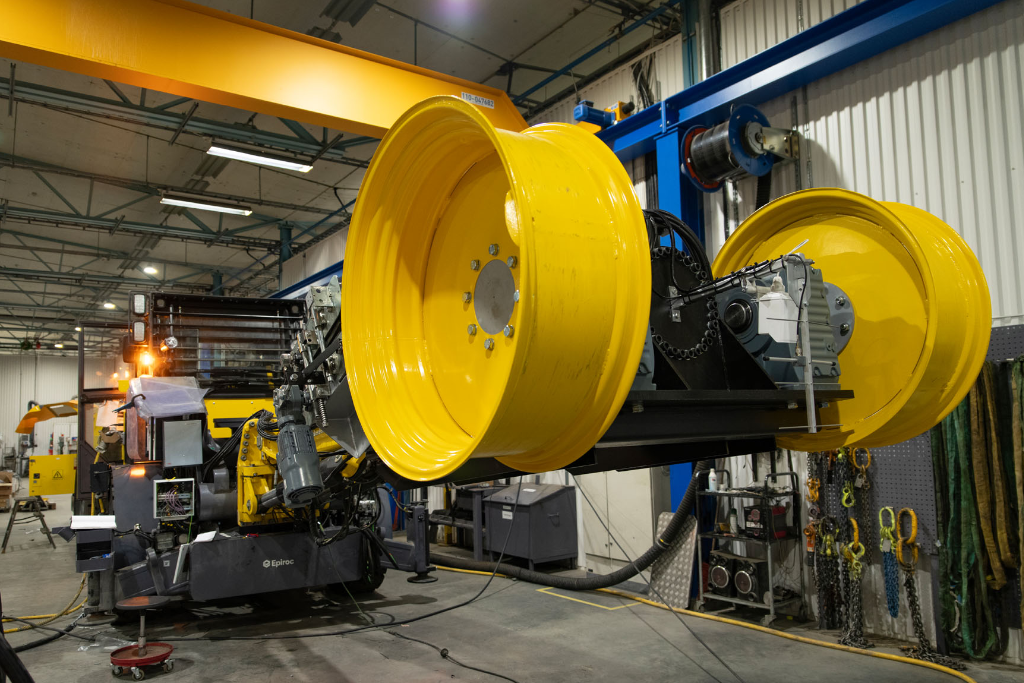
Cable Bolt Rig for shafts has beed developed
A completely unique machine of its kind has been developed by Bergteamet. It will be used for rock reinforcement of narrow shafts where cable bolts are to be installed. The first test of the Shaft Cable Bolt Rig will take place in LKAB’s mine in Kiruna.
Bergteamet’s Shaft Cable Bolt Rig is based on a traditional Epiroc Cabletec that has been modified.
– The concept involves all equipment related to drilling and installation of cable bolt being dismantled and moved to a completely new unit that will be lowered into the shaft and controlled from the base machine, explains Tommy Johansson, foreman at Bergteamet’s workshop.
Many involved in the work
The project has engaged many of the mechanics in the workshop over the past nine months, as well as several partners such as Norrdon, Epiroc, and Komab. The machine is built entirely according to BRAGS regulations.
– It is made in typical Bergteamet spirit. We have worked committedly, persistently, and solved challenges together as they arose. And we have succeeded, says Tommy.
Remote controlled from the machine
The Shaft Cable Bolt Rig is operated by the machine operator from the control unit (original machine unit), which supplies the platform with electricity, water, and control signals. The cable bolt rig unit is lowered and raised in the shaft using a robust fixed hanging scaffolding and an upgraded winch.
There are several benefits with the new Shaft Cable Bolt Rig.
– We make the work safer by removing people from the shaft, but also by being able to use cable bolts that are significantly longer than the shaft’s diameter. This makes the rock reinforcement stronger and able to withstand more, explains Tommy.

Tommy Johansson, arbetsledare vid Bergteamets verkstad.
Complete equipment
The cable bolt rig unit that is lowered into the shaft is fully equipped with all the equipment needed to drill and install the cable bolt into the rock. The cement is mixed on-site with dry mortar and water.
– We also have an emergency device that, for example, allows us to cut off a drill steel or a cable bolt that has gotten stuck, or remotely start a diesel generator if the cable bolt rig unit for some reason becomes powerless, says Tommy.
Fully loaded with concrete, the cable bolt rig unit weighs about 17 tons and is 7.5 meters high. The umbilical cord between the control unit and the cable bolt rig unit is a specially manufactured 1000-volt cable designed for self-hanging in the shaft. The cable is over 220 meters long and contains both electricity to power the cable bolt rig unit and handles communication and control.
Test driving and tuning
The Shaft Cable Bolt Rig was transported from the workshop in Boliden to Kiruna in mid-April 2024.
– The first thing we do on-site is thorough test drives and tuning to ensure everything works as it should and meets our requirements for operational reliability. There will also be training and test driving for the operators, says Tommy.
A Shaft Cable Bolt Rig built on experience
Bergteamet has long experience in shaft works, and the idea of developing a Shaft Cable Bolt Rig has existed for many years, say Mats Ragnarsson and Magnus Bergkvist at Bergteamet.
– We have worked with shaft reinforcement for a long time and have taken several steps in development over the years by developing various remote-controlled equipment, but none as advanced and complete as this one.
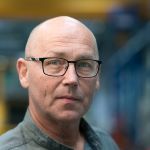
Mats Ragnarsson
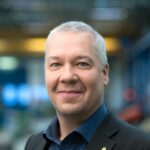
Magnus Bergkvist
The first steps were taken when Bergteamet created its first remote shaft lining robot, which was then followed by the remote-controlled drilling platform used for shaft renovation.
– In connection with this, thoughts arose at LKAB about how to install rock bolts in narrow shafts that have a smaller diameter than the length of the bolts. After some time and some work, we came up with a proposal that LKAB liked, and that’s how it started, says Mats Ragnarsson.
– The advantage of the cable bolt is that it is possible to install cable bolts that are longer than the diameter of the shaft, he continues.
Proven machine with functionality
The choice fell on an Epiroc Cabletec because the machine is familiar and reliable.
– We have good experience with the machine and know it very well. The machine operators are also comfortable with it and know all the functions. It is based on a proven concept that suits us. There is also good availability of spare parts if something should happen. Building something ourselves and controlling it via a control barrack would have been a more expensive solution and required a completely different development process. With an existing machine like a Cabletec, we are convinced that it will work, emphasizes Magnus Bergkvist.
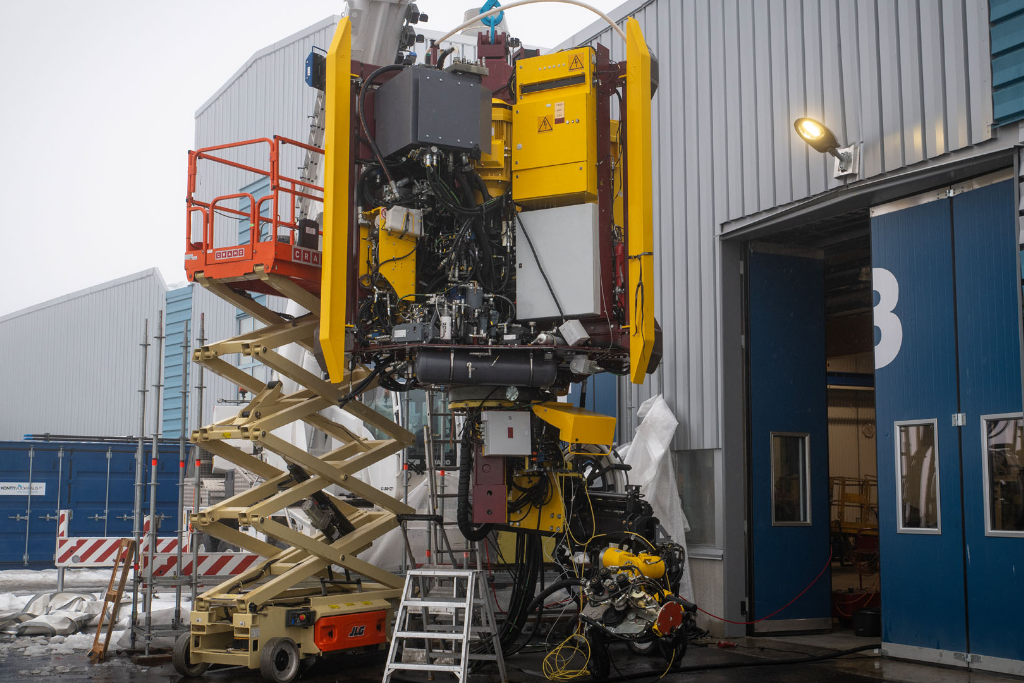
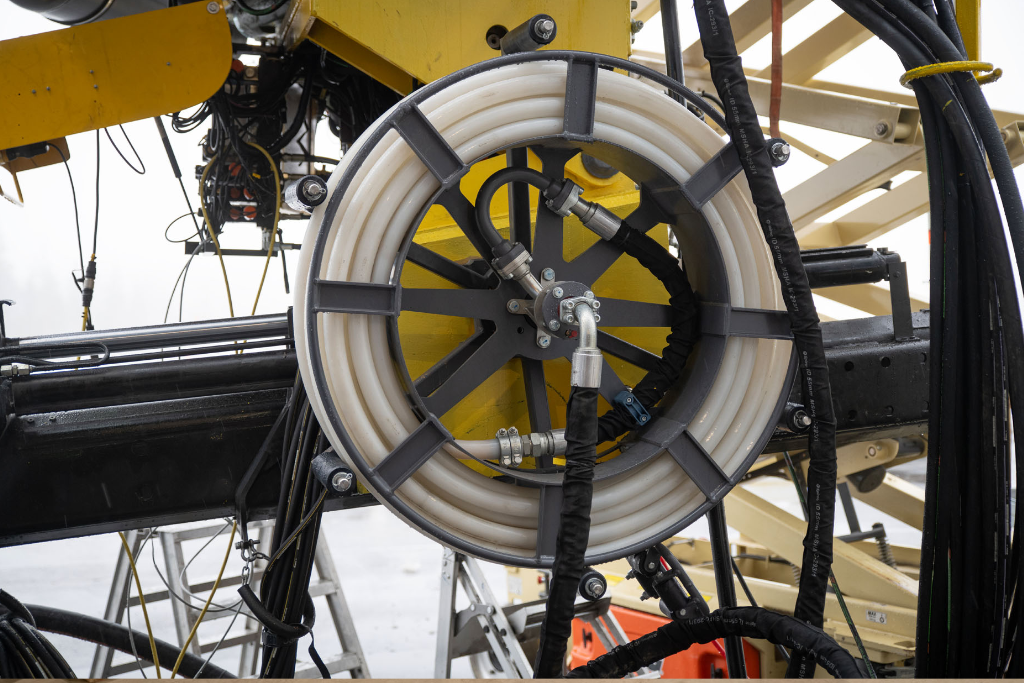
Safe working environment
– The advantages of the machine are not only that it is proven. If the development project turns out well, it will be a safe and efficient solution for strong rock reinforcement of narrow shafts with cable bolts. In addition, many of the risks in the work are eliminated because people do not need to be in the shaft, says Mats.
Wide range of applications
– During 2024, the sharp test will be carried out with LKAB in Kiruna in a recently raise-drilled standing tip shaft that is 145 meters deep. If it turns out well, which we all hope, there will then be many shafts that the Shaft Cable Bolt Rig can be used for, both in Kiruna and in other mines, but also for other projects within infrastructure or hydropower, says Magnus.
All experience gathered
– This is a unique machine that we have been able to develop thanks to our long experience in shaft works and that we, together with our partners, have built and developed everything from remote shaft lining robots, drilling equipment, and shaft hanging platforms. All experience is built into the Shaft Cable Bolt Rig, it is like the crown on the work, emphasizes Magnus Bergkvist.